Supply Chain Management HBR Case Study Help
Hire Someone To Take My Supply Chain Management Case Study
Are You Seeking Employment or Switching Careers? A strong supply chain management case study will improve your chances of employment or switch careers by demonstrating your ability to conduct in-depth research, analyze data and produce actionable insights.
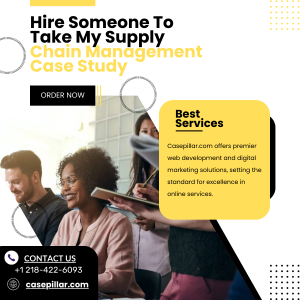
Cincinnati Seasonings provides you with the challenge of meeting customer demand at multiple stores while simultaneously minimizing operating costs and Case Study Help inventory levels. Since these simulations accurately replicate real supply chains, solutions that work in these cases will likely also prove effective for real companies.
Analyze the Issues
Candidates are often called upon to assess the cost and risk associated with any change to a client’s operational configuration. For instance, Recommendation Essay manufacturers with substantial production in China might retain your firm to assess both initial costs and risks associated with moving operations out of there.
Sometimes companies’ supply chains must respond to specific issues like pricing volatility, freight rates or environmental regulations; you are often required to calculate cost sensitivity and identify potential risks before they become show-stoppers. To do this effectively and with visibility across their supply chains it is critical that there be one central point of truth such as using dashboards or alerts to monitor metrics and anticipate any problems before they arise.
Identify the Main Problems
Tracking supply chain data can be a significant burden for some companies. They may struggle to ascertain how much is spent or the costs of particular suppliers; such information is essential for making informed sourcing decisions.
Accurately anticipating consumer demand is another essential aspect of supply chain management. If a forecast falls too low, Maintaining Accessibility a company could end up holding onto excess inventory; conversely if demand spikes, resources may run dry or extra costs will arise for materials.
Time delays are one of the more prevalent supply chain problems, arising from inefficient manufacturing and production processes or inadequate transportation management.
Many companies have been slow to adopt technology designed to streamline supply chain management, which can cause serious complications. Businesses utilizing outdated systems may find it challenging addressing changes in consumer demands or responding to shifts in markets quickly enough.
Examine the Related Problems
Ofttimes, the most efficient way to approach supply chain case studies is to break them down into component parts. Marketers and sales people may understand advertising and sales techniques; however, how a product made its way onto store shelves remains more mysterious to most people.
By breaking down processes into their core elements, people can more efficiently identify problems and develop solutions to them. For example, Innovation At Progressive extra costs might not necessarily stem from storage or transportation expenses but instead be caused by inefficiencies in manufacturing or forecasting processes.
At all stages, it is crucial that you communicate clearly with your interviewer during a case study. This allows them to witness your thought process and correct you if things get off track.
Generate Effective Alternatives
Supply chain cost issues often stem from problems within company culture, forecasting and planning practices or relationships with supply chain partners that need to be overhauled. Achieve this requires time, and having an appropriate process in place can ensure its completion successfully.
An effective Analysis of Alternatives (AoA) requires an objective framework, a clear definition of the need to be fulfilled and a system for assessing alternatives’ effectiveness and viability. Without such a structure, Management Of Globalization there’s always the risk that bias might slip through and undermine its efficacy.
One way to ensure a fair evaluation is to conduct a sensitivity analysis. This involves calculating how a single change to an alternative’s metric score would alter its final ranking and helps identify those most susceptible to any negative changes that may come about; using this methodology helps eliminate bias and ensures an informed choice is made.
Supply Chain Management Case Study Solution
Effective supply chain management ensures that demand meets supply at a minimal cost to business. Insufficient inventory can result in lost sales and Advanced Technology Foundation customer dissatisfaction while excess stock reduces profit margins.
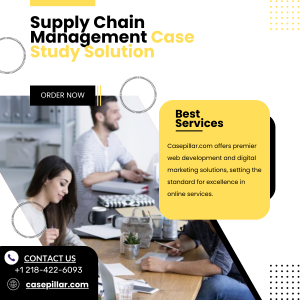
Ranon Logistics Network introduced comprehensive technology into their operations to increase efficiency and profit. The new system significantly reduced order processing times while simultaneously decreasing costs and risk.
Cost Reduction
Companies should strive for holistic cost optimization. Balance fixed and variable costs while optimizing both with technology to streamline business operations and raise cost efficiency. Furthermore, Positive Surveying tracking working capital issues such as inventory hold-ups are vitally important components of financial analysis.
7/11, for instance, regularly analyzes sales data to know which products to place on its shelves each day in order to maximize revenue and keep inventory levels down simultaneously. Another good example is Avaya: this global leader in business collaboration and communications technology had until recently operated what some executives considered an inadequate supply chain network.
Inventory Management
When maintaining an inventory on hand, businesses must carefully consider costs related to storage and insurance as well as theft or obsolescence risks. Furthermore, their products should be delivered quickly to consumers or businesses alike.
Effective supply chain management ensures demand meets or surpasses the production facilities and equipment of a business, including raw materials, subassemblies and components needed at each stage of manufacturing. To meet demand more efficiently this involves planning with software programs to monitor raw materials, Introduction To Financial sub-assemblies and components used during each step in the production process.
An effective business can use its insights about customer preferences to leverage better terms with suppliers and vendors, increase warehouse efficiency and speed order fulfillment, as well as encourage repeat purchases by increasing repeat purchases from repeat buyers and word of mouth advertising. When goods arrive on time to customers it will improve their experience; any lost or delayed deliveries may lead to dissatisfaction and negative reviews for your company.
Inventory Control
Inventory control aims to balance demand with supply at minimal costs to the business. This includes procuring raw materials from suppliers, processing these into outputs and the associated costs of storage or transportation to market.
Reaching this goal requires using data and forecasting to optimize purchasing procedures, reduce inventory carrying costs and set safety stock levels and reorder points. Furthermore, Reinvention Of Learning monitoring inventory levels to detect theft or loss while simultaneously increasing storage capacities to avoid obsolescence is necessary for success.
For security reasons, it is advisable to separate inventory management from accounting and finance. In smaller businesses this could mean creating standard operating procedures or using spreadsheet formulas to track inventory; larger businesses may require special software. No matter their size, successful inventory control requires staff buy-in as well as clear communication throughout the organization: this may include management personnel, procurement specialists, warehouse managers or pickers.
Inventory Forecasting
Marketing and sales may be well understood, but the complex supply chain that brings physical or digital products to customers may remain more mysterious. By breaking it down into its individual steps – raw material to production to delivery to customers – opportunities for improvement can be revealed. Achieve a balance in inventory requires knowing your historical data, Harvard Business Review including peaks and valleys; you can do this using both qualitative or quantitative techniques.
Quantitative forecasting uses historical sales numbers to project future ones and may employ different techniques depending on the length of period being forecasted–be it year, quarter, or month. Visual forecasting plots the same historical data onto graphs that make its peaks and valleys easier to perceive; many prefer it because it can easily interpret trends forecasting results.
Supply Chain Management Harvard Case Solution
An effective supply chain management process keeps companies out of the spotlight and prevents costly product recalls, HBR Case Study while mitigating financial losses due to customer returns.
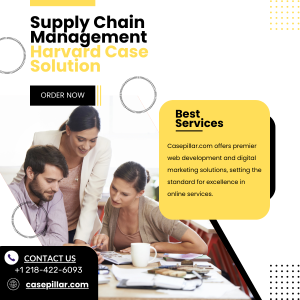
This course introduces students to the theory and fundamental quantitative methods involved in managing global supply chains. Topics discussed include international transportation basics, duties and taxes, trade finance hedging strategies, currency issues and outsourcing.
Problem Statement
With globalization, outsourcing, and increased competition all on the rise, many businesses have come to recognize that supply chain performance is becoming ever more crucial for success. To gain an edge against their competition, organizations need to improve their ability to produce goods more rapidly at reduced costs while simultaneously improving quality.
Supply Chain Management (SCM) encompasses the entirety of the processes necessary for turning raw materials into finished goods and services, from planning, sourcing, manufacturing, Deconstructing Executive transportation and distribution through customer service and product returns.
SCM is heavily influenced by political and economic considerations, including regulations related to environmental protection, employment laws, tariffs, taxes and trade restrictions in different countries. SCM must also take account of cultural influences and socioeconomic trends present across various geographies.
Financial Analysis
A company’s supply chain refers to all the logistical functions involved in developing, manufacturing and distributing their products. An efficient supply chain provides companies with an important competitive edge; its successful functioning involves the transfer of materials, information and capital necessary for production while simultaneously sourcing raw materials and creating distribution channels.
Companies need to find ways of producing high-quality products while simultaneously lowering costs and Personal Career Destination Supply Change Management improving customer service. One strategy for accomplishing this can be accomplished through consolidating previously siloed business functions into an efficient network that enables quick response times to changing market conditions.
Financial analysis is an integral component of supply chain management. This process examines items on a profit and loss statement for their relationship to overall business performance, and helps identify weaknesses and strengths to enhance future results. Financial analysis may also save companies money by helping avoid costly mistakes that lead to delays in shipment; and it can prevent customer churn due to missed deliveries.
Environmental Factors
Companies strive to reduce the negative environmental impacts associated with their supply chains, including using less hazardous materials and decreasing energy usage and carbon emissions.
Finding opportunities for improvement is one of the greatest challenges companies face, yet many organizations are working towards this end through initiatives like responsible sourcing, Bridges For Economic Growth green transportation and adopting cloud computing technologies. Finding people capable of driving change may also prove to be challenging as this requires multiple parties – including company leadership, employees, suppliers and their representatives – being engaged.
An essential aspect of crisis management is understanding how to mitigate risk during an outbreak. This is particularly relevant during pandemics where there are numerous risks that could threaten supply chains; such as social distancing, self-isolation and travel restrictions which could create severe disruptions. Luckily there are tools which can assist businesses in recognizing these threats as early warning signals while mitigating any negative impacts they might have on supply chains and environments alike.
Legal Factors
Supply chain management must account for legal considerations, such as compliance with environmental regulations and human rights laws. This is especially essential for companies operating internationally as their supply chains must abide by varying sets of laws in various countries.
An organization producing textiles must make certain its suppliers adhere to all national occupational health and safety requirements, Non Profit Corporation which includes providing adequate training and instructions to employees as well as paying them fair wages. Furthermore, child labor should not be exploited in any form by suppliers.
Human rights due diligence must also be conducted on all suppliers regardless of where they’re based, given how more consumers and investors are becoming concerned with sustainability footprints of companies – including conditions in their supply chains. Law departments play an essential role here by reviewing supplier contracts to ensure they align with company sustainability standards.